Early years
The birth of machinery specialized trading company YKT
1908Keizo Yamamoto started working at an American-import trading company
The founder of YKT, Keizo Yamamoto, joined the American trading company Andrew George, where he worked as sales of imported machine tools. During this time, he achieved success by delivering the first Gleason gear cutting machine in Japan to The Imperial Steel Works (a UNESCO World Heritage site: Sites of Japan's Meiji Industrial Revolution).
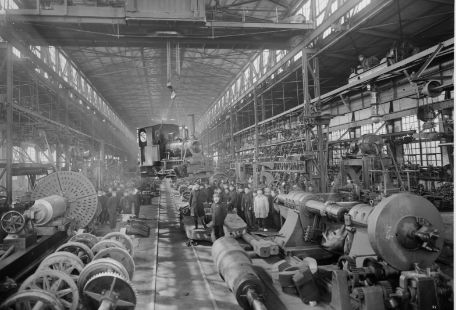
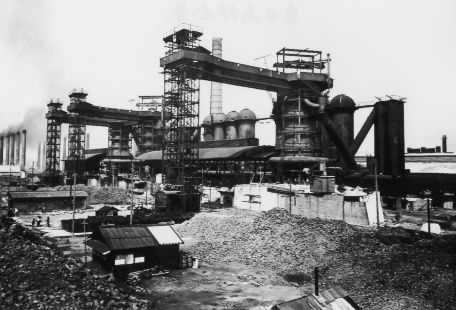
Image provided by NIPPON STEEL CORPORATION.
1914After being a prisoner of war, Gustav Rudolf worked for a German machinery trading company in Japan.
Gustav Rudolf, a German, became a prisoner of war during the Battle of Tsingtao in World War I and was interned at the Bando Prisoner of War Camp in Tokushima Prefecture. At the Bando Camp, he was given opportunities such as baking bread and pastries and playing musical instruments. He became an instructor in gymnastics and a member of the Engel Orchestra, forging friendships with local residents. After Germany's defeat, he remained in Japan and worked for Carting, a German trading company specializing in import of German machine tools.
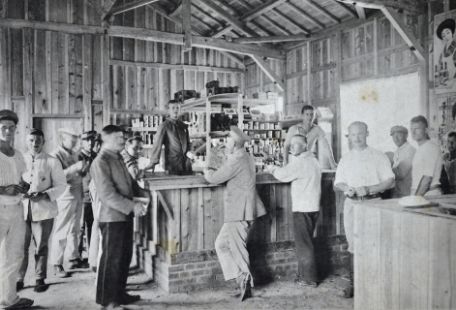
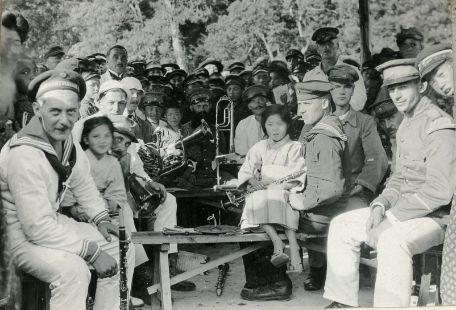
Image provided by the Naruto German House
1924The encounter with Mr. Rudolf leads to the establishment of Yamamoto Shokai.
In the aftermath of the Great Kanto Earthquake in 1923, the president of Akashi Seisakusho, Kazue AKASHI (later CEO of Koganei), relocated the factory in Asakusa to the Marunouchi Building 7 in Tokyo, where he began importing and selling German and Swiss machinery. Drawing inspiration from imported material testing machines, Mr. Akashi, who aimed to focus on precision equipment manufacturing, approached his long-standing acquaintance Mr. Yamamoto in order to transfer the import machinery sales business to him. He also introduced Mr. Rudolf, the head of the machinery department at the Carting Trading Company, which was struggling with low sales due to the recession at the time and had a large inventory. As it was difficult for the American-owned Andrews & George Company to sell German machine tools, Mr. Yamamoto left the company and established Yamamoto Shokai in Tsukiji, starting the sales of imported German machines. The establishment of a system where Carting Trading Company handled import while Yamamoto Shokai handled sales was solidified after the disposal of the large inventory held by the former. German machine tools were highly regarded by major users for their superior precision compared to domestic machines and their stable accuracy over long-term use.
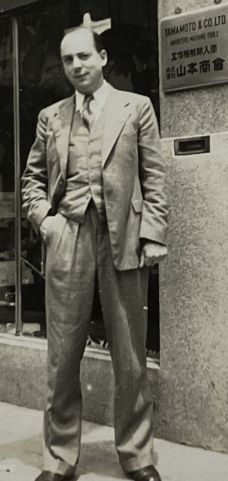
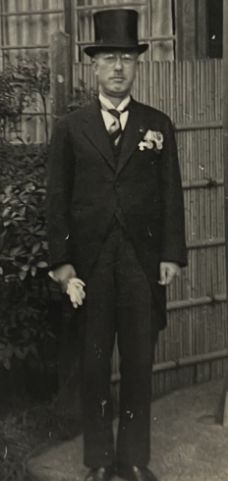
1926Sales of INDEX machines
Through Hahn und Kolb, two INDEX Type 0 machines were sold in Japan. The Trans-Siberian Railway was used for transporting the machines, allowing them to reach Japan in 2-3 weeks. INDEX lathes were utilized for processing diesel engine injection nozzle components for military use. When the Second World War made machine transport via the Trans-Siberian Railway difficult, modified military submarines and U-boats were used to transport INDEX machines to Japan, while alloy metals were shipped from Japan and the Pacific region to Germany. Over 900 INDEX automatic lathes were delivered in Japan, with most sold before the 1960s when Japanese-made lathes rapidly gained competitiveness, resulting in a decline in INDEX machine sales in Japan. We began handling INDEX machines since the year following our company’s founding, and we remain their sole distributor up to 2024. In 2014, INDEX celebrated its 100th anniversary, and we have been the longest-running distributor, maintaining our partnership for a century.
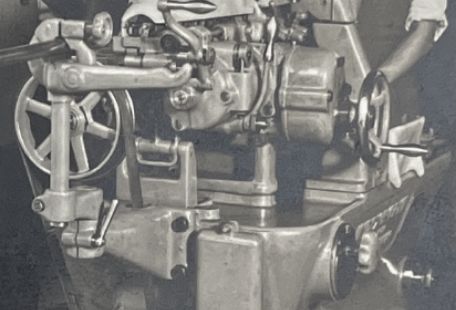
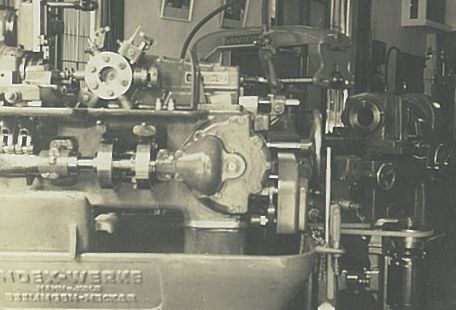
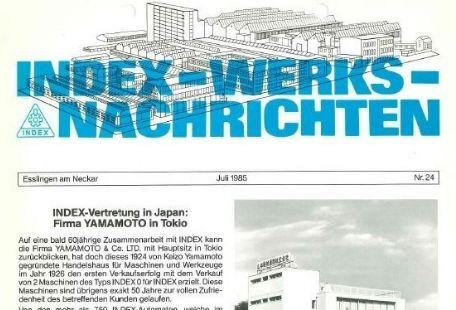
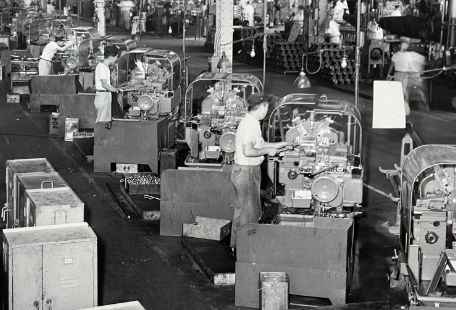
1933Acquisition of import agency rights
When the Nazis prosecuted the Jewish Mr. Carting, it hindered Carting Trading Company’s ability to import machine tools. With Yamamoto providing some of the funds, Mr. Rudolf decided to acquire the commercial rights of Carting Trading Company, thus allowing Yamamoto Shokai to obtain the import agency rights. Yamamoto Shokai actively sent employees for training in Germany and Switzerland and engaged them as sales engineers. By offering installation and technical guidance, they gained high trust from users unfamiliar with foreign-made machines. Yamamoto Shokai instilled in its employees the philosophy of "Be proactive and meticulous" as a guiding principle.
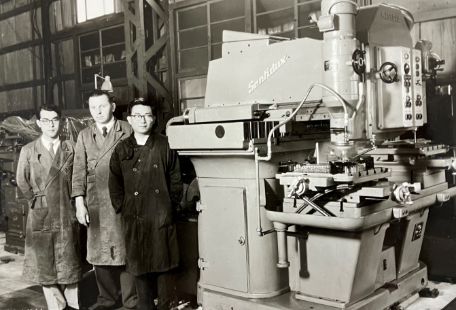
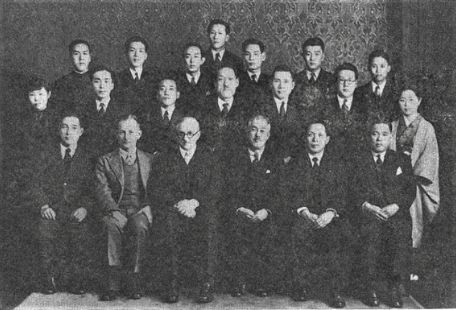
Center right: Keizo YAMAMOTO
Our Products
Our Customers
Other Photos
Decision making period
Escape from adversity and new opportunities
1939Approach of World War 2 and starting manufacturing business
Amidst the looming signs of war in Europe, Mr. Yamamoto visited manufacturers in Germany and Switzerland aboard the Haruna Maru from Kobe Port in January, returning via the United States in September. During his visits, he became intent on starting a manufacturing business, and he urgently sent a telegram from Germany to prepare land for a factory, and Yamamoto Trading secured land in Koganei. Anticipating the increase in difficulty of importing machinery, arrangements were made with manufacturers for purchase of equipmentt for their own production facilities, with efforts made to expedite shipment. As World War II erupted and maritime transport became difficult, transportation shifted to overland transport via the Siberian Railway. With the onset of the German-Soviet War, the transport of machinery became hopeless, and continuing the import machinery business became challenging.
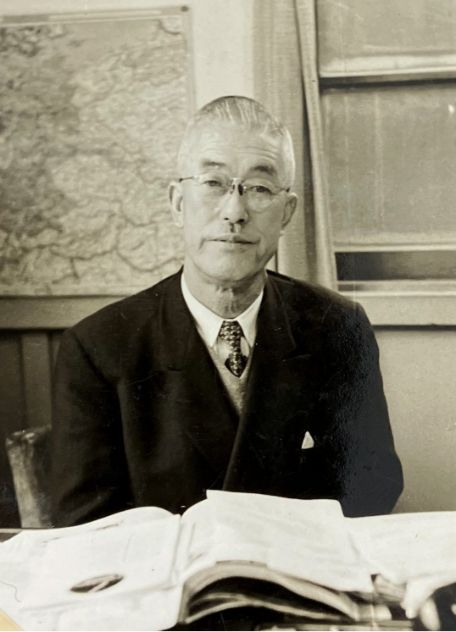
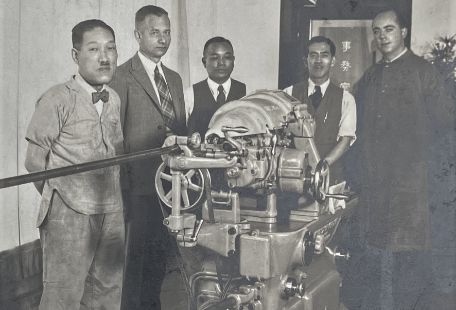
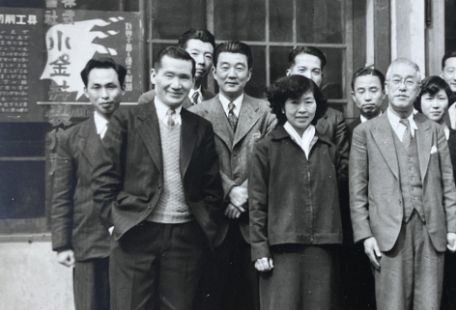
1941Start of manufacturing precision tools
With the cease of machinery imports, Yamamoto Trading changed its name to Yamamoto Kogyo. Due to increasing military demand, it began handling domestic machinery. Imported machinery was installed at the Koganei factory, and in response to requests from the Japanese military, manufacturing of precision tools commenced. Products such as spiral broaches for cannon barrels, chamber reamers for machine guns, and plug gauges were manufactured, primarily delivered to the Naval Air Headquarters. At the time, Kenji Yajima, who would later become a selected artist of the Japan Art Exhibition (Nitten), worked as a conscripted laborer. A portrait of Keizo Yamamoto painted by him still hangs in the reception room of the Tokyo headquarters.

by Kenji Yajima
1943Key to machinery transport in the turbulence of war
From Germany, large submarines were used to import weapon schematics and machine tools, with some machinery transported by submarine as well. Even resorting to using submarines, the desired machinery was available through Yamamoto Trading's business partners. One such machine was the Franz Braun horizontal injection molding machine "Isoma" from Germany. Records exist of the Isoma machine being transported to Yokohama Port by submarine U-boat through Yamamoto Trading.
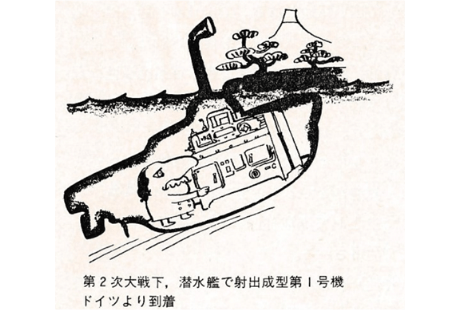
by SEKISUI CHEMICAL CO.,LTD.”
Column
The Isoma Machine, the Foundation of Injection Molding Machines in Japan
Japan acquired radar technology from Germany, which was ahead in pulse radar technology. High-frequency characteristics were necessary for radar components, which required plastic injection molding machines. Isoma machines were transported to Japan by U-boats for the transfer of pulse radar technology. After the war, it became the prototype of Japan's horizontal injection molding machines, making significant contributions to the development of Japan's plastic injection molding industry.
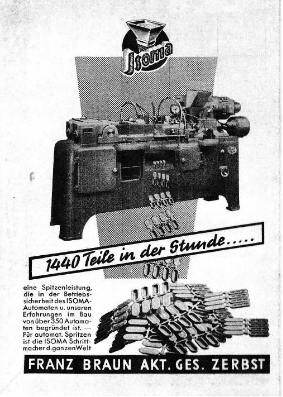
1949Resuming of import and sales of machine tools
After the war, as the demand for precision tools declined and international trade resumed, Yamamoto Kogyo separated the import and sales of machine tools from its operations and reestablished Yamamoto Trading. Branch offices were opened in Osaka and Nagoya, resuming the import and sales of machine tools. Yamamoto Trading and its separate division, which was manufacturing precision tools in Koganei, evolved into Koganei Corporation, a comprehensive manufacturer of pneumatic and hydraulic equipment, which continues to this day (as of 2024).
On the other hand, Mr. Rudolf returned to Germany after the war and, together with his colleague Mr. Von Appen, established Von Appen & Rudolf Trading Company. Based in Hamburg, they handled exports from Germany, while Yamamoto Trading handled imports in Japan, establishing a sales route for German machine tools.
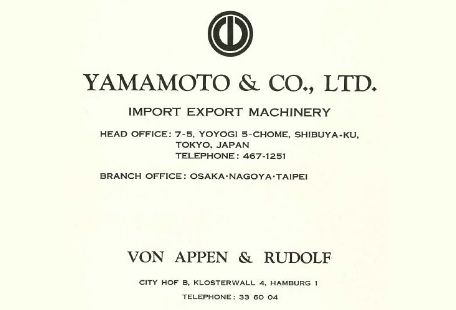
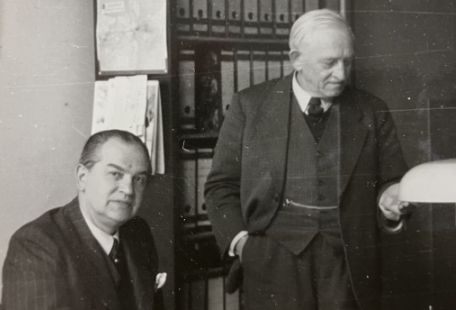
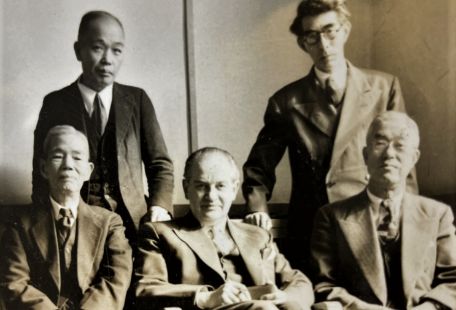
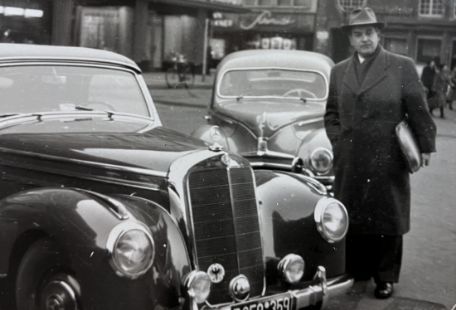
Column
Post-War European Manufacturers Situation
After the war, Mr. Von Appen immediately visited their pre-war business partners but lost the distribution rights for Swiss jig grinders from HAUSER during the post-war confusion. INDEX machines were imported from Hahn & Kolb, which was both a sales and manufacturing company, but after the war, INDEX established its own sales company, initiating direct transactions between INDEX and Von Appen & Rudolf Trading Company. British Small Armours (BSA), a manufacturer of small single-axis automatic lathes, received INDEX's production equipment and blueprints as part of war reparations, resulting in the production of British-made INDEX machines.
Furthermore, the division of Germany into East and West led to the transfer of ZEISS IKON's microscope manufacturing blueprints and engineers to the Soviet Union, where Soviet-made imitation microscopes emerged. During the Cold War, trade between Japan and the Soviet Union often involved barter transactions, resulting in the importation of a large number of microscopes from the Soviet Union to Japan. For about 20 years, from the late 1960s to the late 1980s, our company sold the UIM microscopes from MASHPRIBORINTORG with Japanese-made scales attached and precision readjustments made.
However, in the late 1980s, the introduction of groundbreaking camera-based measuring machines from the United States, a Cold War adversary, led our company to begin handling these new measuring machines and withdraw from the sale of Soviet-made microscopes.
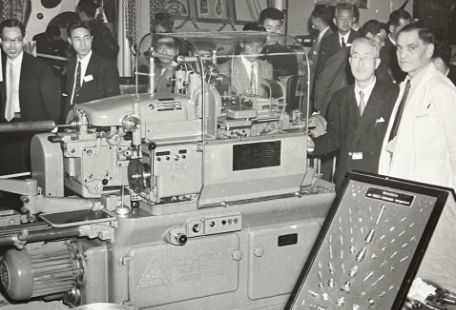
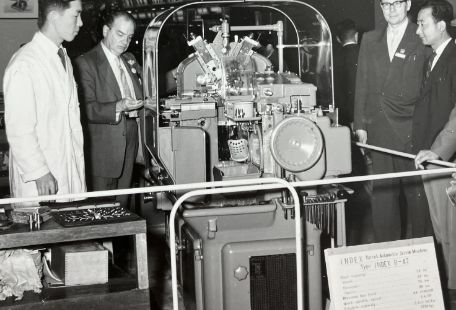

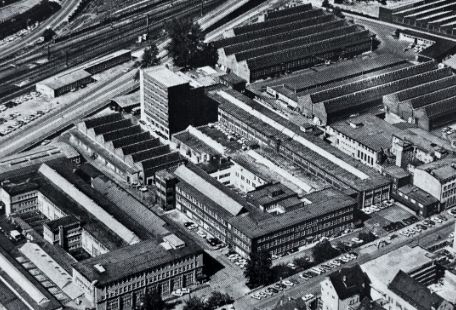
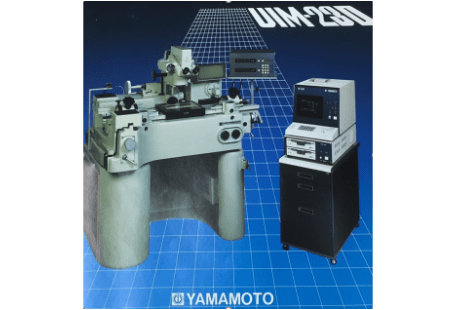
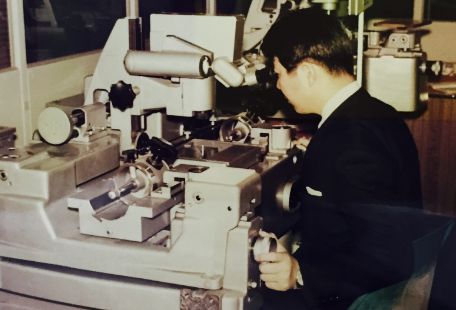
1962Participating in the first JIMTOF
With the outbreak of the Korean War in 1950, Japan entered a period of reconstruction. At that time, domestic machine tools suffered from poor materials, leading to early wear of guideways and rapid degradation of accuracy. As a result, imported machine tools capable of maintaining superior accuracy over an extended period were in high demand. In 1952, with the government granting subsidies for imported machine tools, the sale of imported machine tools became increasingly bustling. In 1954, Yamamoto Trading exhibited an INDEX single-axis lathe at the Japan International Trade Fair, showcasing industrial products. Subsequently, this trade fair was held alternately in Osaka and Tokyo each year and evolved into a biennial specialized exhibition for machine tools. The first Japan International Machine Tool Fair (JIMTOF) was held in Osaka in 1962. Our company has been continuously exhibiting at on-site JIMTOF thanks to our customers’ support.
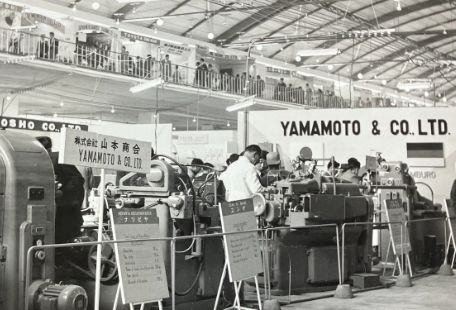
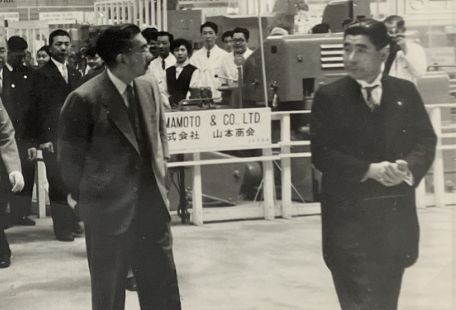
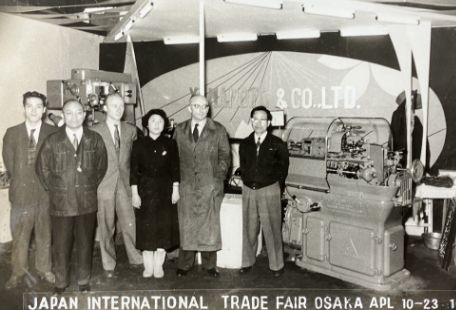
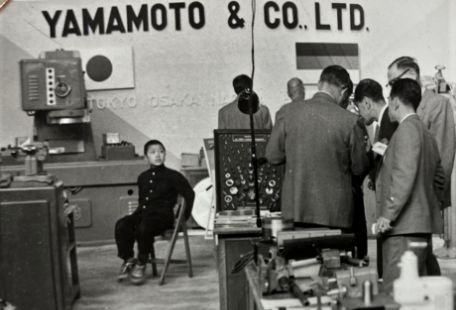
1967Changing the company name to Yamamoto Machinery Trading and starting sales of domestic machine tools
In the 1960s, under government subsidies, many excellent Western machine tools were imported for the purpose of imitation. Furthermore, domestic machine tool manufacturers significantly improved their performance by actively engaging in technological partnerships with advanced Western machine tool manufacturers. In 1967, Yamamoto Trading relocated its headquarters to the vicinity of Yoyogi-Hachiman Station on the Odakyu Line and changed its name to "Yamamoto Kikai Tsusho" (Yamamoto Machinery Trading). A domestic business department was established, and sales and exports of competitive domestic machine tools commenced. At that time, while there were internal discussions regarding the sales of domestic machine tools, which competed with imported ones, the following passage remains in the company guidebook:
Following the natural law of water flowing from high to low, we import high-tech measurement equipment and industrial machinery, while exporting domestic machinery with high potential energy.
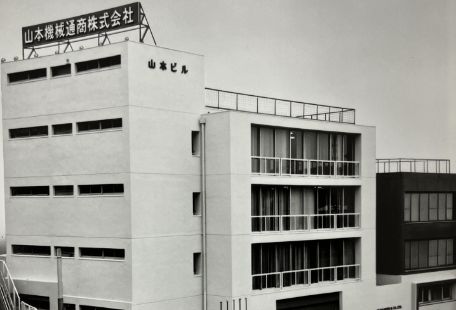
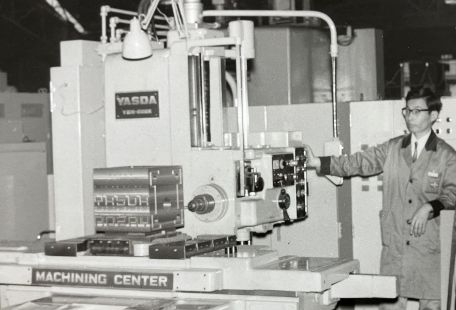
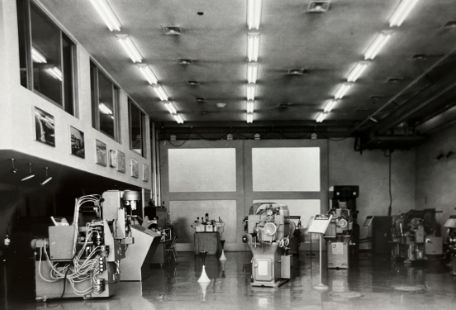
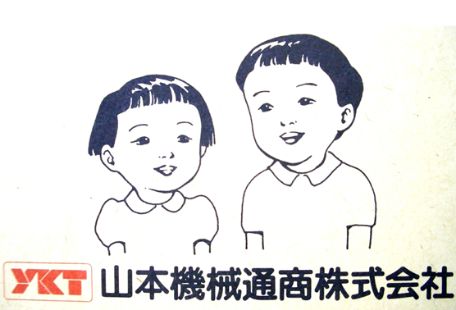
1977Parting Ways with Von Appen & Rudolf Trading Company
From its establishment until 1977, machinery was sold through the intervention of two trading companies, one for export and one for import, between manufacturers and users. However, with the improvement in quality of domestic machine tools, sales became challenging. Following discussions, Von Appen & Rudolf Trading Company and Yamamoto Machinery Trading agreed to propose to German machine tool manufacturers the option to choose between an export trading company and an import trading company through a joint written document. Instead of mutual collapse, a decision was made to simplify the trade flow, leading to their parting ways. Few German manufacturers would choose an import trading company in Japan, located in the Far East; most of them opted for Von Appen & Rudolf Trading Company, which had been their main point of contact. Machine manufacturers such as Gebrueder Heller and Carl Hurth , which were the main suppliers to the automotive industry at the time, gradually distanced themselves from Yamamoto Machinery Trading. Von Appen & Rudolf Trading Company later changed its name to Rudolf Trading Company and established a local subsidiary in Japan, but withdrew from machinery sales in Japan in 1994.
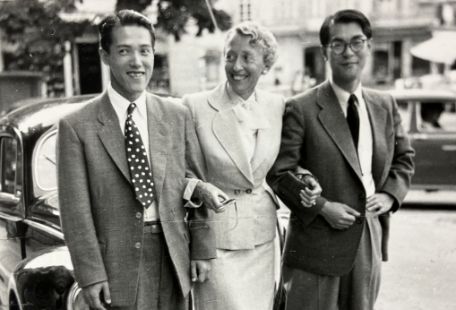
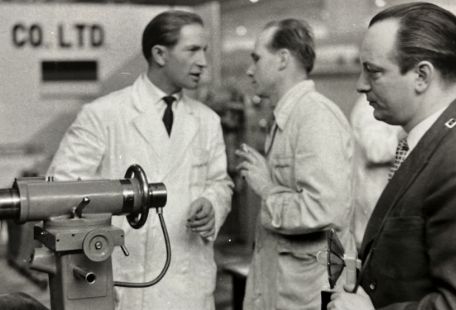
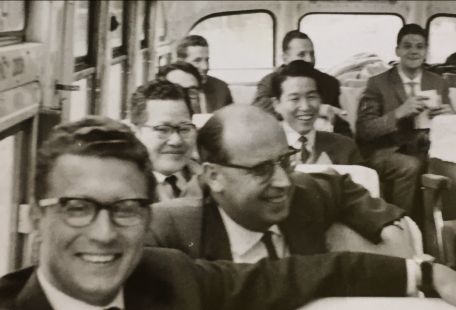
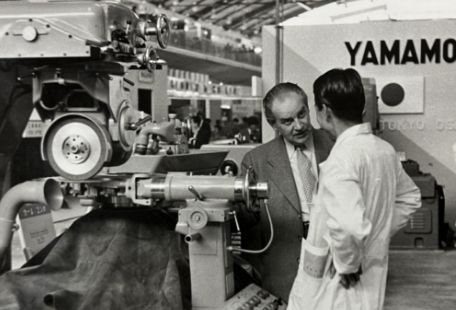
Our Partners
Former Partners
Other Photos
Transformation period
Encounter with Cutting Tools, Measurement, and Electronics Industry Products
1977Opening of German office
Due to the split with Von Appen & Rudolf Trading Company, our base in Germany ceased to exist. Consequently, we decided to establish a new office in Germany. With the help of the automatic lathe manufacturer INDEX, we set up our office in Ostfildern Ruit, a town adjacent to Esslingen in southern Germany where the INDEX company headquarters is located.
1981Hosting the Yamamoto Europe Tour ‘81
Based on the belief that, despite superior machine performance, final accuracy of the workpiece depends on cutting tools, our company embarked on product development for the cutting tool industry. In order to have European machinery evaluated by domestic tool manufacturers familiar with cutting tools, the first tool tour was organized in 1981. Among the main destinations of the tour was Rollier, who was the predecessor of Rollomatic, manufacturing point grinding machines for producing microdrills. The tour at the time was summarized as follows: "In the future, convincing users to introduce the highest European technology will become increasingly difficult. Only specialized trading companies that can connect manufacturing experts with end users can handle imported machinery."
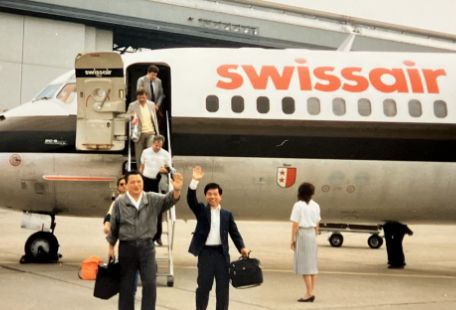
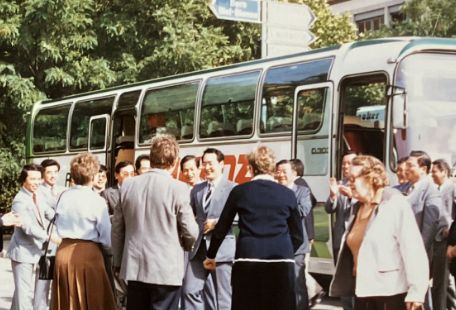
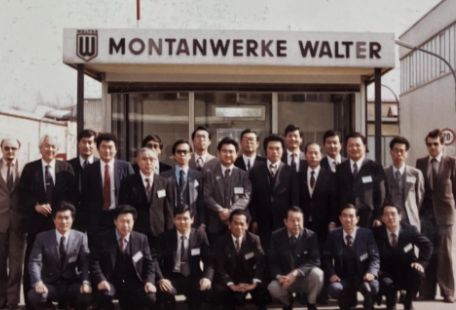
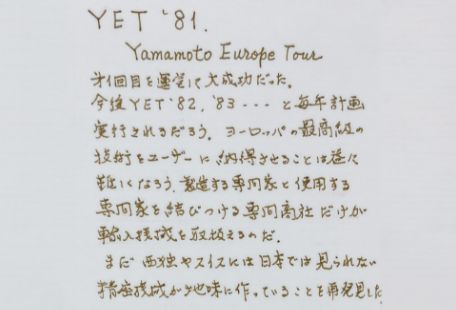
1981Signed an exclusive agency agreement with Rollier following the YET '81 tour
One of the destinations on the YET '81 tour was Company Rollier, the predecessor of Rollomatic, which manufactured and sold small-diameter drills and grinders. The company initially engaged in the manufacturing of watch parts but found that high-quality tools were not available on the market. This led them to manufacture small-diameter tools themselves, which gained a good reputation among industry peers. The machine they developed, called "Roll-O-Matic," was a drill point thinning grinder sold mainly in Germany and Switzerland.
At that time, Japanese cutting tool manufacturers were struggling with runout issues. They observed part-time female workers at Rollier easily producing small-diameter drills with minimal runout. The runout control of their tools was achieved through a guide bush support method with a tolerance range of a few microns. Due to the high evaluation of the Roll-O-Matic, there was a rush of requests to purchase the machines.
Initially, Rollier was reluctant to sell their machines in Japan, but gradually the path to sales in Japan was opened.
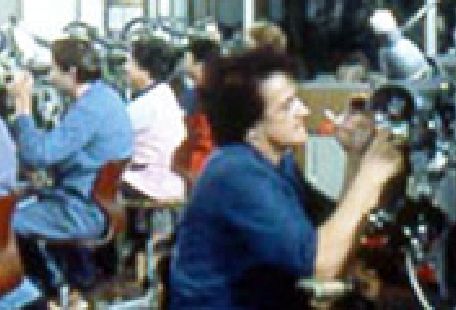
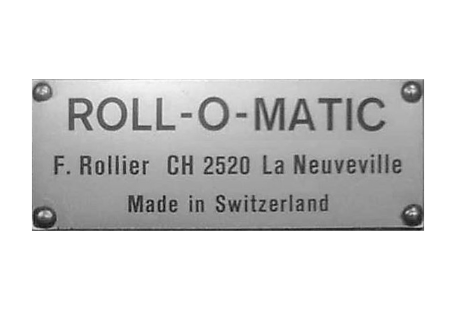
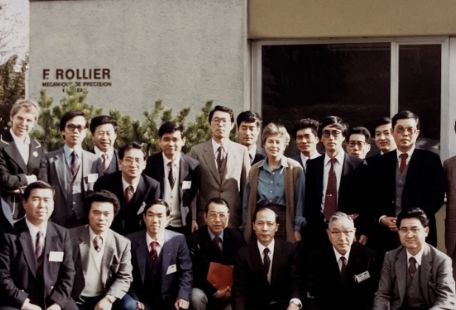
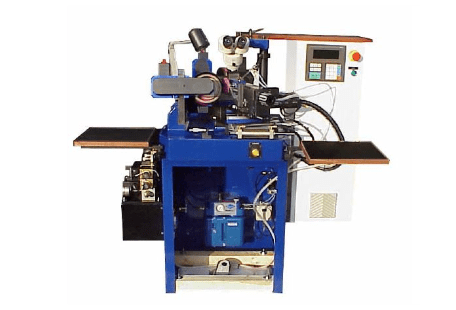
1982Entering the electronics industry
The production engineering division of Kyushu Matsushita Electric, formerly located on Minoshima Island in Fukuoka Prefecture, was a user of surface grinding machines from the German manufacturer Carl Jung Machine. On the other hand, we provided sales support for their winding machines, particularly automatic assembly devices for automobiles. With the start of surface mounter production by Kyushu Matsushita Electric, our challenge to the electronics industry began as a sales agent for mounters. With the spread of electronic products such as video games, mobile phones, CD players, and personal computers, surface mounters became high in demand. Furthermore, Kyushu Matsushita Electric's surface mounter "CREATE" boasted industry-leading high-speed and high-precision capabilities, receiving high praise from many domestic users. In the 1990s, surface mounter production shifted to Taiwan, and then to China from the 2000s onwards. During this transition, our company established subsidiaries in Taiwan and China, laying the groundwork for expansion into the Chinese-speaking region. Kyushu Matsushita Electric's FA Division was integrated with the FA Division of Matsushita Electric Industrial Co., Ltd. in 2003, and we have continued to maintain business relationships with the newly joint company under the name Panasonic Connect (as of 2024).
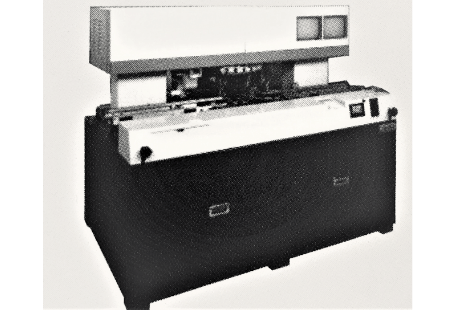
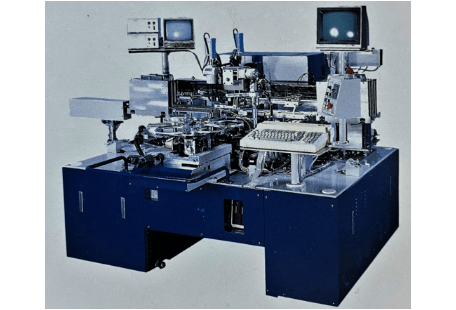
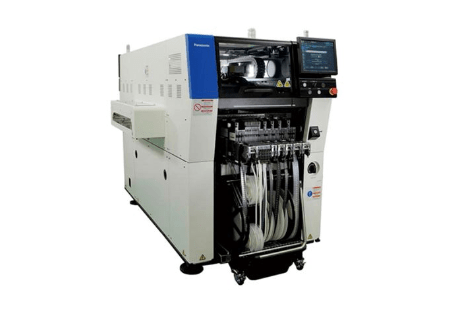

1988The miracle of ‘88
In 1983, we began handling video camera-type measuring machines from the American company OGP. These were very expensive products, and the concept of measuring images captured by video cameras was not yet widely recognized in the market, leading to difficulties in sales. OGP, dissatisfied with the sales figures, became increasingly concerned as sales of similar Japanese-made products began. As a condition for continuing the partnership, we were required to sell 10 units over the next year.
Two favorable conditions emerged at this point, pushing our company forward. Firstly, the introduction of the new Q-SEE series was significant. With a shift from pulse motors to servo motors, these machines enabled agile measurements and were designed with improved usability for on-site operations. At that time, the term "turbo" was popular, and the agile measurement operations of the Q-SEE series were described as "turbo". Additionally, in 1988, during the economic bubble, there was a boom in capital investment. The heightened competitiveness of the product and the flourishing market environment were fortunate factors, as sales, which had been limited to two units in 1987, skyrocketed to an astonishing 19 units in 1988. Thanks to this miracle in 1988, our partnership with OGP continued.
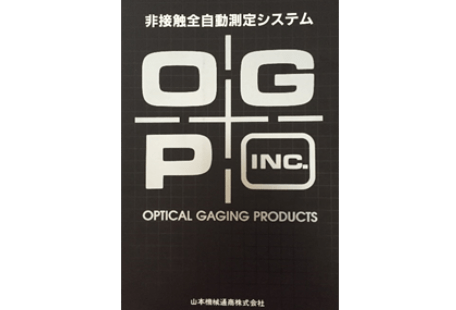
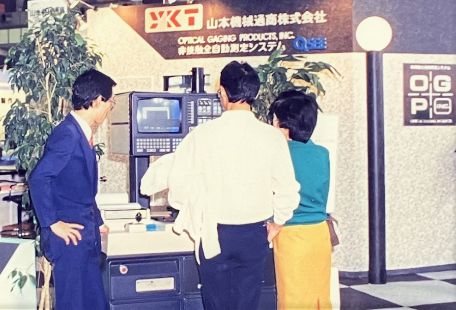
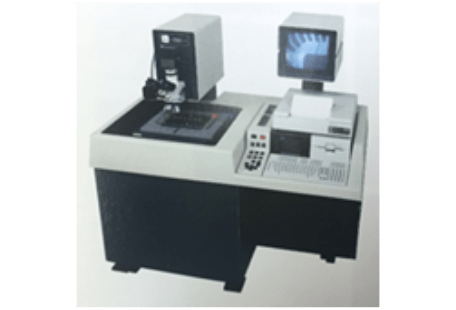
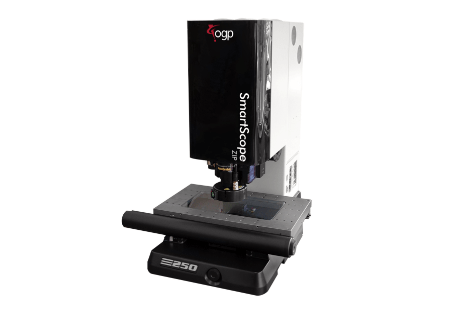
1992Completion of the Nagoya Office Building
The construction of our own building for the Nagoya office was completed, including a showroom. We established a demonstration system for imported machine tools and measurement equipment, aiming to strengthen our sales presence in the Chubu region.
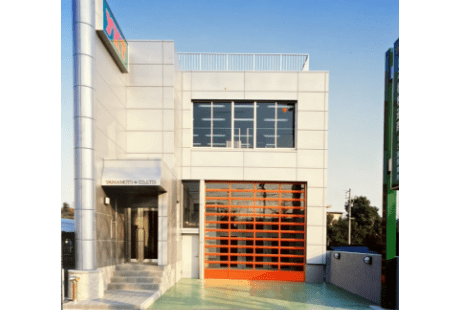
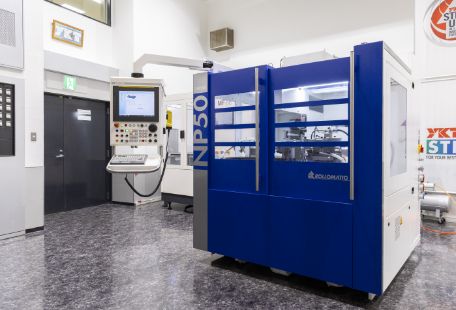
1996Opening of Taiwan office
Amidst the shift of surface mount production from Japan to Taiwan in the 1990s, we opened a local office in Taipei, Taiwan.
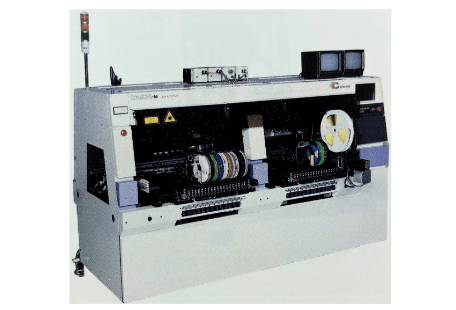
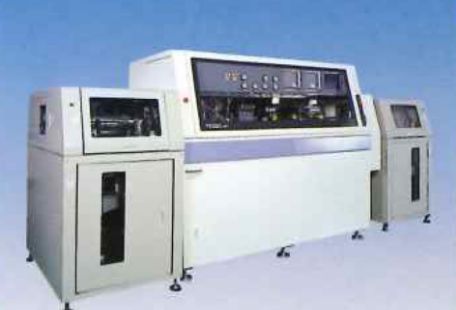
Other Photos
Expansion period
Corporate Growth and Establishment of Overseas Bases
2001Over-the-counter registration with the Japan Securities Dealers Association
Following the termination of securities business by Japan OTC Securities Co., Ltd., we listed on the JASDAQ Securities Exchange (Tokyo Stock Exchange Standard as of 2024). As part of our strategy to establish growth, development, and sustainability, we went public with our stocks. The public offering enabled us to secure talented personnel and strengthen our financial foundation.
2001Establishment of YKT Shanghai
With the formal accession to the WTO, the market was liberalized in China, where we decided to establish an office in Shanghai. This was to expand our sales and service support in response to the full-scale shift of the electronics industry to China.
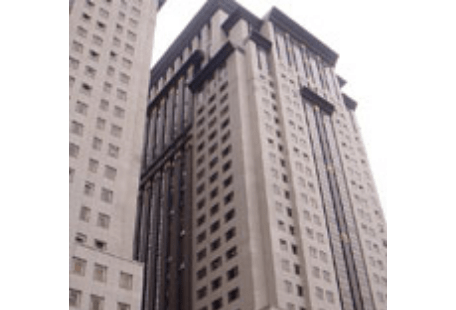
2002Changing the company name to YKT
Due to the revision of commercial registration, registration of the company name in Roman letters became possible. As part of our efforts to adopt a global company name, we changed our registered name to "YKT".
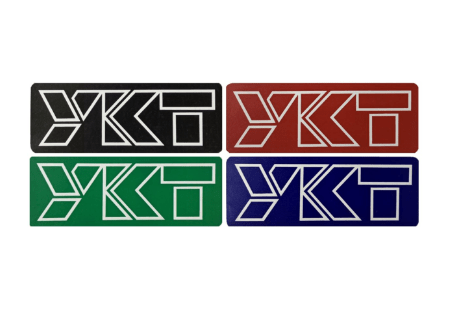
2002Subsidiarization of Sun Instruments
In the growing market of the telecommunications sector alongside the trend of digitization, we expanded our product range and thus subsidiarized Sun Instruments, an import trading company specializing in laser, optical communication equipment, and spectrometers.
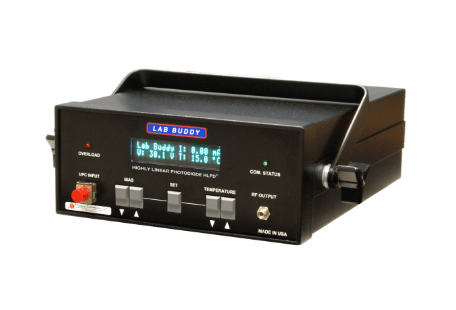
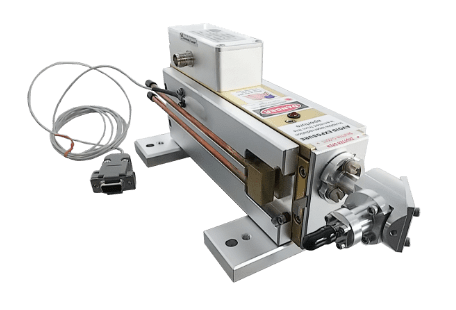
2002Start of joint project with Nissho Machinery
As a joint project with Nissho Machinery, we began the development and sales of peripheral devices for display mounting machines, such as conveying devices and terminal cleaning machines. In 2009, we expanded our lineup to include display mounting machines, which have been adopted in smartphones, tablets, laptops, and automotive displays, and are sold primarily in the Chinese-speaking region.
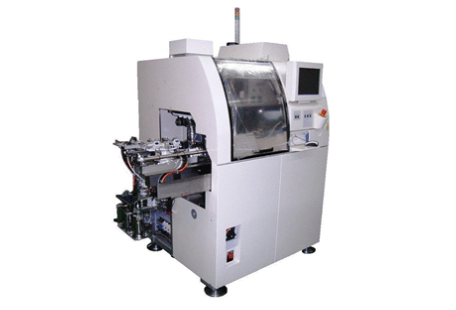
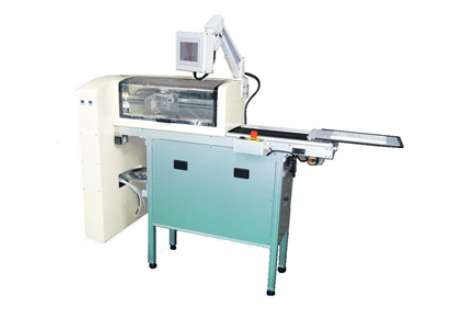
2003Acquisition of ISO14001
To reduce the environmental impact arising from our business activities, we obtained ISO 14001 certification for our environmental management system.
2005Establishment of YKT Europe
To strengthen support for transactions with European manufacturers, and to facilitate the development and sales of new products in the European region, we established a local subsidiary by incorporating our German office. As part of our global strategy and to serve as a base in Europe, we established YKT Europe near Stuttgart.
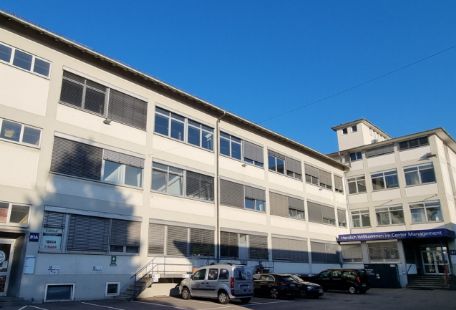
2005Completion of the Osaka Office Building
To ensure profitability for each base, we restructured both the Nagoya and Osaka sales offices into branches. A self-owned building with a showroom was completed for the Osaka branch, with the aim of stabilizing revenue. To achieve this, half of the building was utilized as residential apartments. We also established a demonstration system for imported machine tools and measurement equipment to strengthen sales efforts in western Japan.
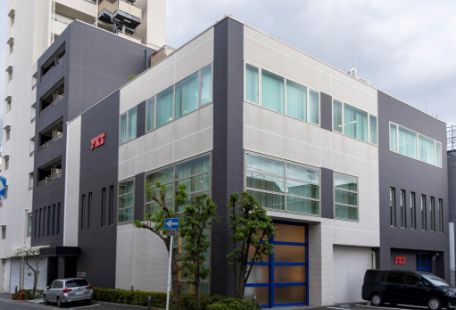
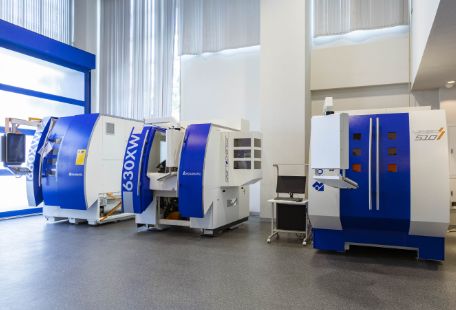
2006Establishment of YKT Taiwan
To expand our business in the electronics equipment sector, we incorporated our Taiwan office and established YKT Taiwan in Taipei. We built a direct sales and service support system for our Taiwanese customers.
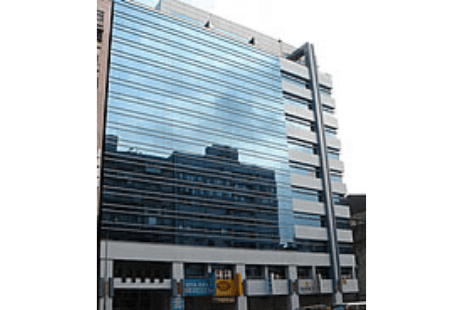
2015Establishment of YKT Thailand
To cater to the rapidly growing Southeast Asian market, YKT Thailand was established in Bangkok, Thailand, where many Japanese companies are expanding their presence. It serves as a sales base for machinery and industrial equipment as well as measurement equipment in the ASEAN region.
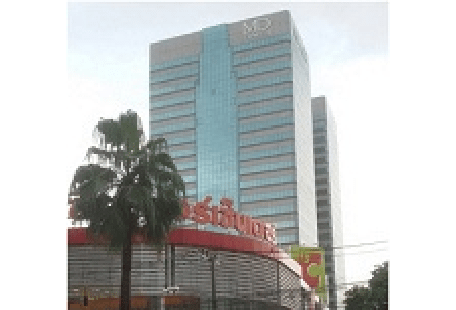
Other Photos
Innovation period
Bringing fresh air to internal regulations and environment
2018Opened a demonstration center in Chofu City, Tokyo
Since it was found to be difficult to install a showroom during the reconstruction of our headquarters building, we established a demonstration center in Fuchu instead. This facility is not only for showcasing measurement equipment but also for conducting demonstrations, providing a well-prepared environment.

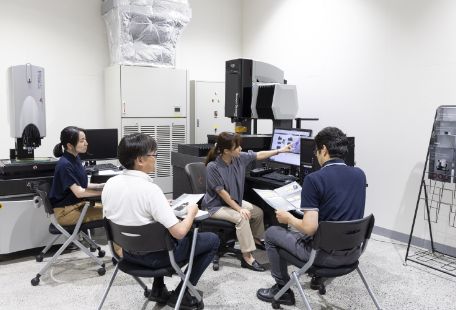
2020Completed construction of a new headquarters building in Shibuya Ward, Tokyo
The construction of our new 7-story headquarters in front of Yoyogi-Hachiman Station on the Odakyu Line was completed. The first floor is designated for retail shops, while the 4th to 7th floors are utilized as offices for startup companies.
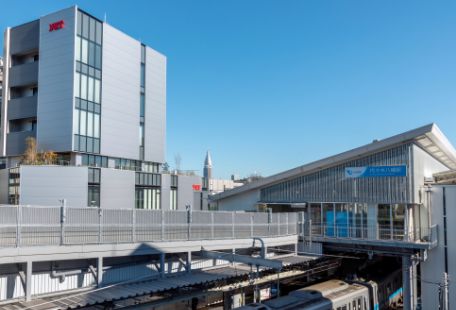
2020Started development of semiconductor mounting equipment
We expanded the functionality of terminal cleaning machines for display mounting, as well as mounting machines compatible with OLED, LCD, and silicon panels. In addition, we started development of semiconductor mounting equipment and made a full-fledged entry into the semiconductor mounting industry
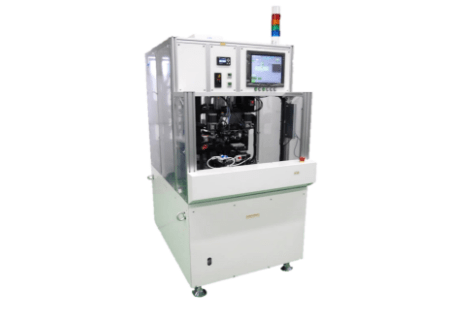
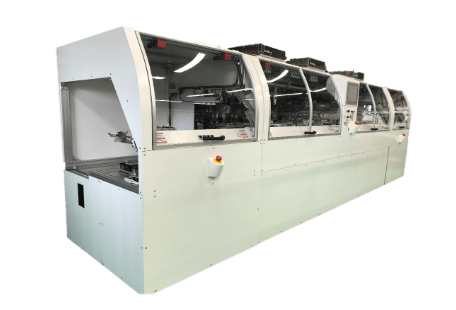
2023Started development of mounting equipment for microLED displays.
We have developed mounting equipment for microLED displays, which are gaining attention as the next-generation displays following LCD and OLED, due to their high purity color of LED that reaches the eye directly and excellent utilization efficiency of light resulting in low power consumption. We aim to provide advanced solutions in the related mounting processes to adapt to the evolution of display technology.
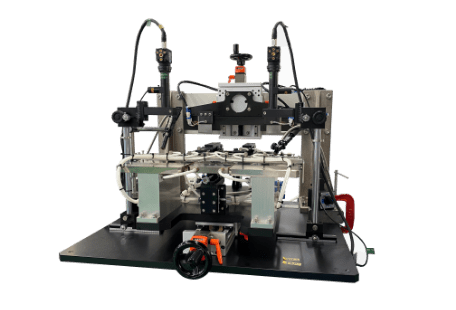